Scannable Pro Turns One!
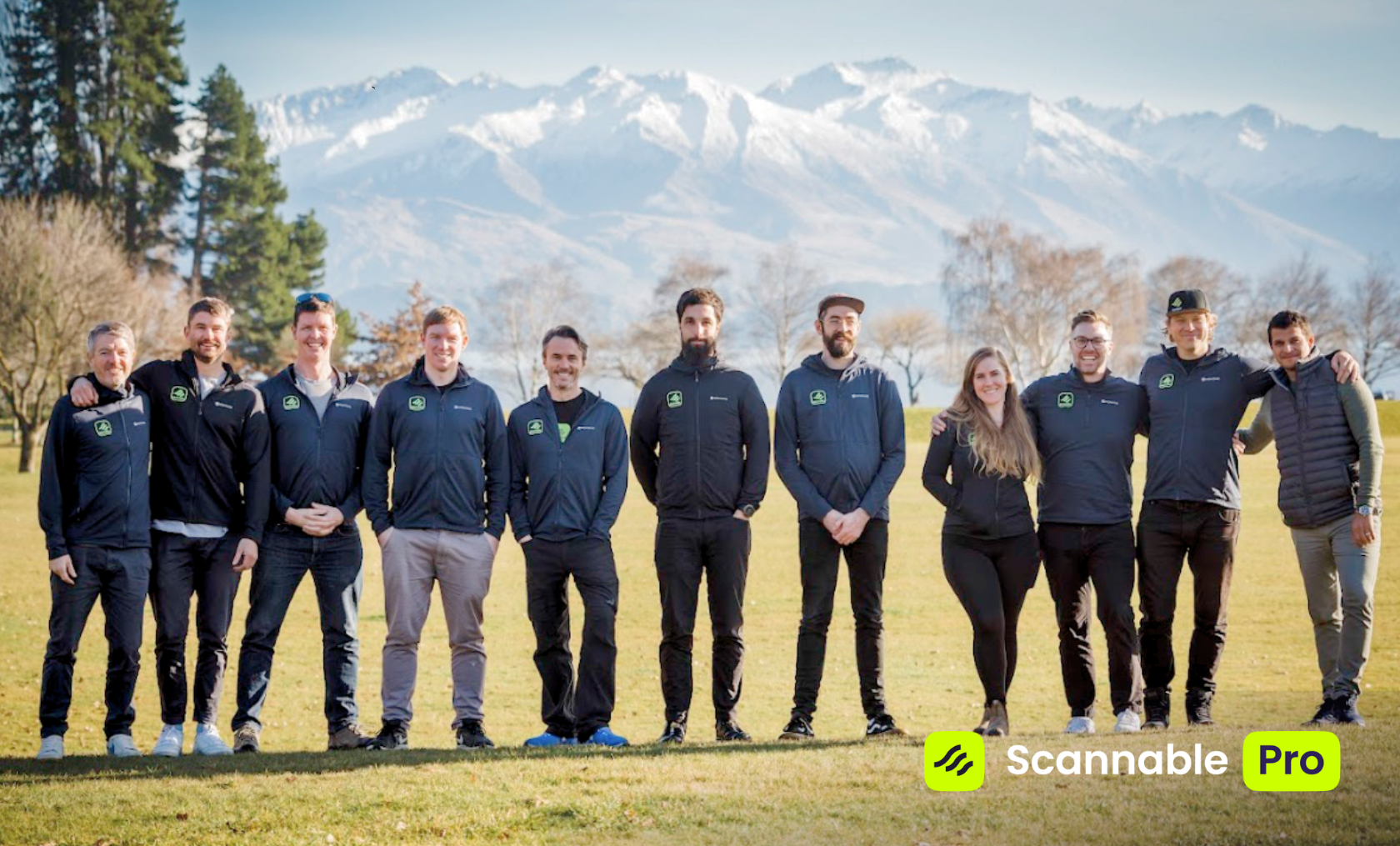
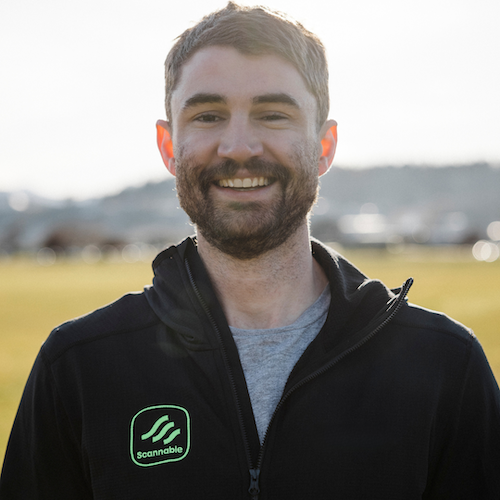
About the author:
Many of you will have had the pleasure of chatting with Matt O’Neill. His excitement to be part of Scannable’s journey and taking an innovative and impactful idea global has not faded since day one. Matt loves being immersed in the world of working at height and enjoys being a driver of Scannable’s powerful engine that is breaking down health and safety barriers in an under-served industry.
Scannable Pro, our equipment management solution for teams and organisations, turns one this month!
To celebrate, we’re suiting up in our finest flameproof PPE (Scannable purple, naturally) to blow out a candle and reflect on why hundreds of organisations around the world now trust us with their safety.
We recently heard a story from one of our UK retail partners about how this Petzl Grillon safety alert impacted two of their customers: one being a Scannable user (let’s call them Bob), while the other, who we’ll call Jim, is not using Scannable.
Jim had to issue a stop-work notice while every technician manually checked their equipment to see if they had an affected Grillon, wasting hours and costing thousands.
Bob, on the other hand, logged into the Scannable web-app and searched for 'Grillon,' sorted by Date of Manufacture, and confirmed they were in the clear—all in under 2 minutes. Plus, we had already emailed them about it.
.png)
I chat with organisations facing similar challenges every day as a result of not having an effective safety equipment management system in place.
These challenges aren’t limited to a specific region, industry, or type of organisation, and can be distilled into three main problems:
- Managing and inspecting safety equipment is manual and time-consuming
- Tracking safety equipment as it moves around the organisation is tough—gear goes missing and replacement costs are high
- Compliance risk is high because inspections are missed and gear isn't tracked accurately.
These problems come at the expense of time, money and most critically, safety.
This isn't news to us. Our co-founder, Rob, heard these concerns from day one.
Addressing these issues is at the heart of Scannable's mission to provide the most efficient and connected PPE management experience in the world.
So, how has Scannable Pro helped organisations streamline their safety processes over the past year? Let’s dive into three key ways.
Scannable Pro has Saved Time on Equipment Management
Many organisations that have joined Scannable Pro over the past 12 months have come from a spreadsheet-based headache and moved into an efficient, user-friendly platform.
Spreadsheets were designed for bookkeeping after all—not PPE management.
The motivations for moving to Scannable are variations of the same theme: old systems are time-consuming, manual, error-prone, and don’t scale; and people are tired of inputting long, faded, serial numbers into spreadsheets to record inspections or assign equipment to a technician or a job. And then repeating this process over and over… and over again.
Our customers report that using Scannable has seen a reduction in time taken to manage a single item by up to 80% thanks to phone-scannable equipment and a super-simple inspection or assignment workflow.
.png)
We’ve swapped out manual data entry for a single tap of your phone, which is just one way we drive efficiency through simplicity.
We’ve designed Scannable Pro with the user-experience at heart, and are proudly enabling our customers to focus on tasks that truly deserve their time and skill… which doesn’t include entering the wrong serial into a spreadsheet four times.
Scannable Pro has Reduced the Cost of Gear Loss
No matter big or small, every organisation I talk to is amazed at how safety equipment seems to grow legs and vanish. The consensus is that this is frustrating, and losses hurt the bottom line year after year.
While we can’t promise that Scannable will completely stop gear from disappearing, we can leave a trail of breadcrumbs so you at least know where to start looking. Knowing things like the location the equipment was last assigned to and who it was last scanned by point you in the direction of tracking things down.
Three ways we see our customers keeping track of their gear with Scannable are:
- Assigning equipment to a team member, or a group like a Kit Bag, Location, Client, or Vehicle
- Using the ‘Check-off’ feature to scan gear against a manifest (like a Kit Bag) and identify exactly what’s come back from a job, and what hasn’t
- Viewing an item's history to see where it is supposed to be, and who was last to scan it. Taking it one step further, you’ll soon be able to see the geolocation of that last scan.
Scannable Pro has Reduced Compliance Risk
I’ll often ask folks who are considering Scannable to compare the cost of one day of shutdown due to non-compliance against the cost of Scannable for a year (hint: Scannable stacks up pretty well).
If you’ve ever had to produce inspection records for an audit or workplace investigation, you’ll know how important it is to trust that your records are up to date and accurate, and that you can pull reports in a timely manner.
This is a concern that pervades spreadsheet users—Inspection data is touched by so many hands, it can’t be relied on to be 100% accurate and true.
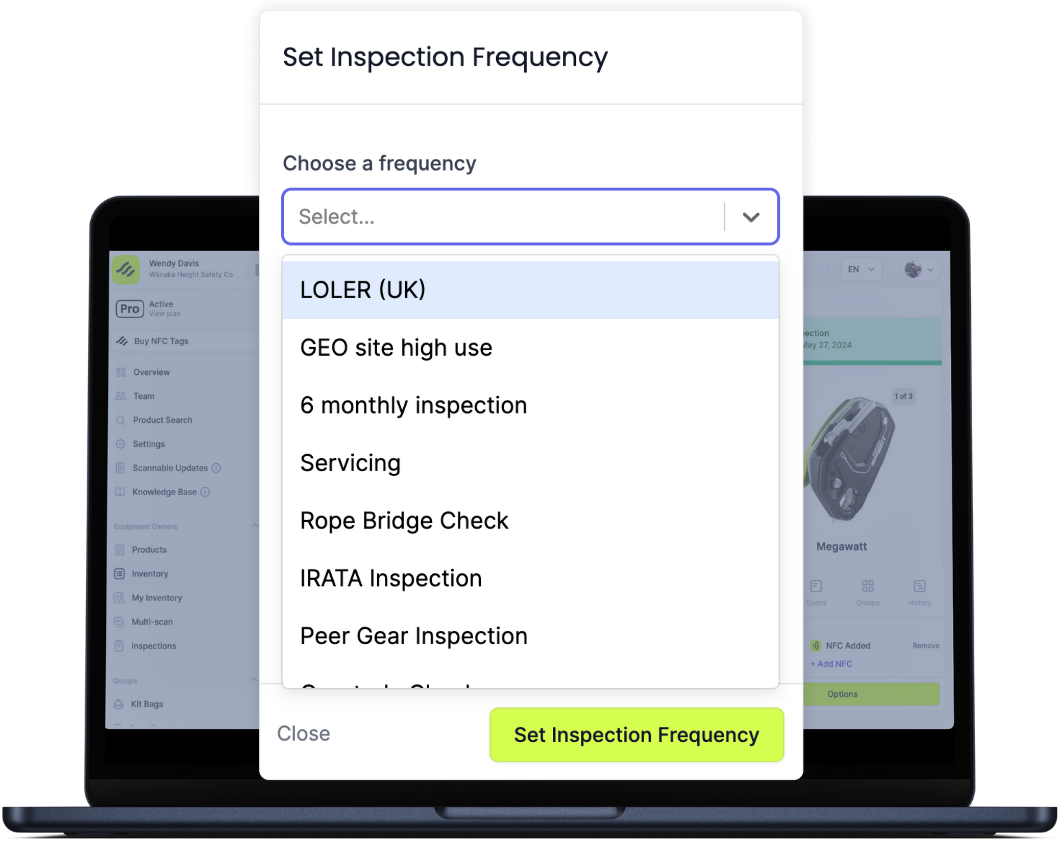
Scannable Pro helps you never miss an inspection with the ability to set inspection frequencies, and (soon) alerts—though this is a fundamental part of any safety compliance system, and isn’t necessarily unique.
What is unique is the ability for anyone with an NFC-enabled device to view an item’s information via its public URL (or webpage), something that every item on Scannable has, no app or account required. All inspection history and technical product data is available to you (or your auditor) with a tap of your phone or a simple shared link.
And the report that proves compliance of all equipment you’re using on a client’s site? Available in PDF with one-click.
.png)
More Equipment to Choose From=Less Data Entry.
It’s been a big 12 months for our safety equipment database too, having doubled in size from 22,000 to 45,000! Next stop, 100k?
If you've got an item you want to add to your inventory but can't find it in our database, let us know! We'll get it added for you ASAP.
That rounds out just three of the ways that we’ve helped our customers solve their safety equipment management challenges in year one, and I’m so excited to see what we add to this list in years to come.
To all of our customers, thank you for being part of the journey!
To anyone on the fence, it will only take us 15 minutes to figure out whether Scannable can help or not. Book a time for chat with me here.
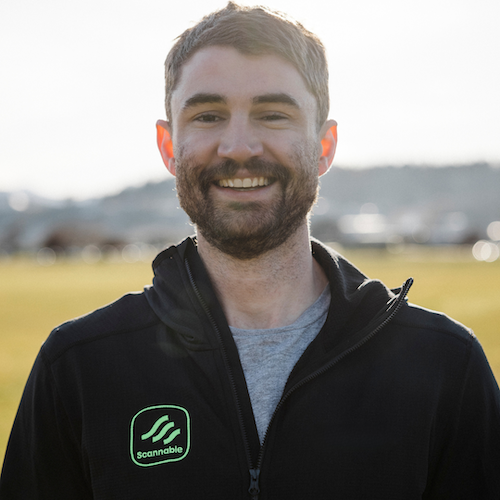
About the author:
Many of you will have had the pleasure of chatting with Matt O’Neill. His excitement to be part of Scannable’s journey and taking an innovative and impactful idea global has not faded since day one. Matt loves being immersed in the world of working at height and enjoys being a driver of Scannable’s powerful engine that is breaking down health and safety barriers in an under-served industry.
Scannable Pro, our equipment management solution for teams and organisations, turns one this month!
To celebrate, we’re suiting up in our finest flameproof PPE (Scannable purple, naturally) to blow out a candle and reflect on why hundreds of organisations around the world now trust us with their safety.
We recently heard a story from one of our UK retail partners about how this Petzl Grillon safety alert impacted two of their customers: one being a Scannable user (let’s call them Bob), while the other, who we’ll call Jim, is not using Scannable.
Jim had to issue a stop-work notice while every technician manually checked their equipment to see if they had an affected Grillon, wasting hours and costing thousands.
Bob, on the other hand, logged into the Scannable web-app and searched for 'Grillon,' sorted by Date of Manufacture, and confirmed they were in the clear—all in under 2 minutes. Plus, we had already emailed them about it.
.png)
I chat with organisations facing similar challenges every day as a result of not having an effective safety equipment management system in place.
These challenges aren’t limited to a specific region, industry, or type of organisation, and can be distilled into three main problems:
- Managing and inspecting safety equipment is manual and time-consuming
- Tracking safety equipment as it moves around the organisation is tough—gear goes missing and replacement costs are high
- Compliance risk is high because inspections are missed and gear isn't tracked accurately.
These problems come at the expense of time, money and most critically, safety.
This isn't news to us. Our co-founder, Rob, heard these concerns from day one.
Addressing these issues is at the heart of Scannable's mission to provide the most efficient and connected PPE management experience in the world.
So, how has Scannable Pro helped organisations streamline their safety processes over the past year? Let’s dive into three key ways.
Scannable Pro has Saved Time on Equipment Management
Many organisations that have joined Scannable Pro over the past 12 months have come from a spreadsheet-based headache and moved into an efficient, user-friendly platform.
Spreadsheets were designed for bookkeeping after all—not PPE management.
The motivations for moving to Scannable are variations of the same theme: old systems are time-consuming, manual, error-prone, and don’t scale; and people are tired of inputting long, faded, serial numbers into spreadsheets to record inspections or assign equipment to a technician or a job. And then repeating this process over and over… and over again.
Our customers report that using Scannable has seen a reduction in time taken to manage a single item by up to 80% thanks to phone-scannable equipment and a super-simple inspection or assignment workflow.
.png)
We’ve swapped out manual data entry for a single tap of your phone, which is just one way we drive efficiency through simplicity.
We’ve designed Scannable Pro with the user-experience at heart, and are proudly enabling our customers to focus on tasks that truly deserve their time and skill… which doesn’t include entering the wrong serial into a spreadsheet four times.
Scannable Pro has Reduced the Cost of Gear Loss
No matter big or small, every organisation I talk to is amazed at how safety equipment seems to grow legs and vanish. The consensus is that this is frustrating, and losses hurt the bottom line year after year.
While we can’t promise that Scannable will completely stop gear from disappearing, we can leave a trail of breadcrumbs so you at least know where to start looking. Knowing things like the location the equipment was last assigned to and who it was last scanned by point you in the direction of tracking things down.
Three ways we see our customers keeping track of their gear with Scannable are:
- Assigning equipment to a team member, or a group like a Kit Bag, Location, Client, or Vehicle
- Using the ‘Check-off’ feature to scan gear against a manifest (like a Kit Bag) and identify exactly what’s come back from a job, and what hasn’t
- Viewing an item's history to see where it is supposed to be, and who was last to scan it. Taking it one step further, you’ll soon be able to see the geolocation of that last scan.
Scannable Pro has Reduced Compliance Risk
I’ll often ask folks who are considering Scannable to compare the cost of one day of shutdown due to non-compliance against the cost of Scannable for a year (hint: Scannable stacks up pretty well).
If you’ve ever had to produce inspection records for an audit or workplace investigation, you’ll know how important it is to trust that your records are up to date and accurate, and that you can pull reports in a timely manner.
This is a concern that pervades spreadsheet users—Inspection data is touched by so many hands, it can’t be relied on to be 100% accurate and true.
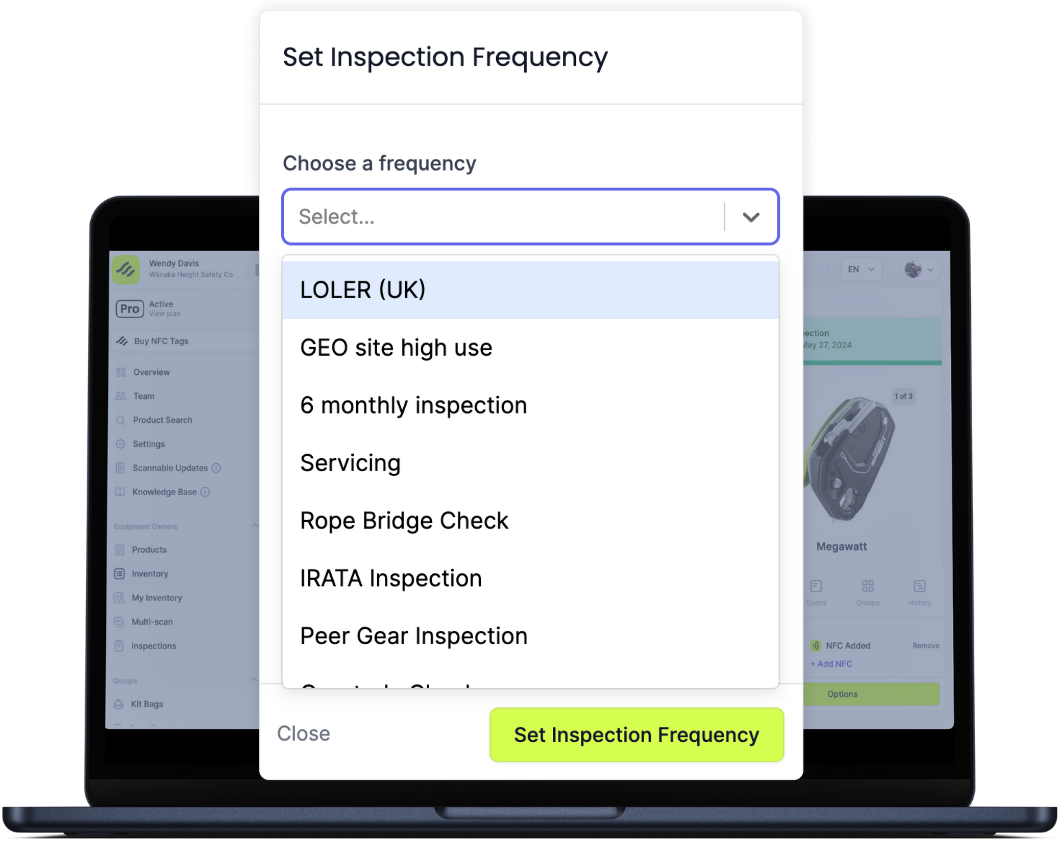
Scannable Pro helps you never miss an inspection with the ability to set inspection frequencies, and (soon) alerts—though this is a fundamental part of any safety compliance system, and isn’t necessarily unique.
What is unique is the ability for anyone with an NFC-enabled device to view an item’s information via its public URL (or webpage), something that every item on Scannable has, no app or account required. All inspection history and technical product data is available to you (or your auditor) with a tap of your phone or a simple shared link.
And the report that proves compliance of all equipment you’re using on a client’s site? Available in PDF with one-click.
.png)
More Equipment to Choose From=Less Data Entry.
It’s been a big 12 months for our safety equipment database too, having doubled in size from 22,000 to 45,000! Next stop, 100k?
If you've got an item you want to add to your inventory but can't find it in our database, let us know! We'll get it added for you ASAP.
That rounds out just three of the ways that we’ve helped our customers solve their safety equipment management challenges in year one, and I’m so excited to see what we add to this list in years to come.
To all of our customers, thank you for being part of the journey!
To anyone on the fence, it will only take us 15 minutes to figure out whether Scannable can help or not. Book a time for chat with me here.