Why we're building Scannable
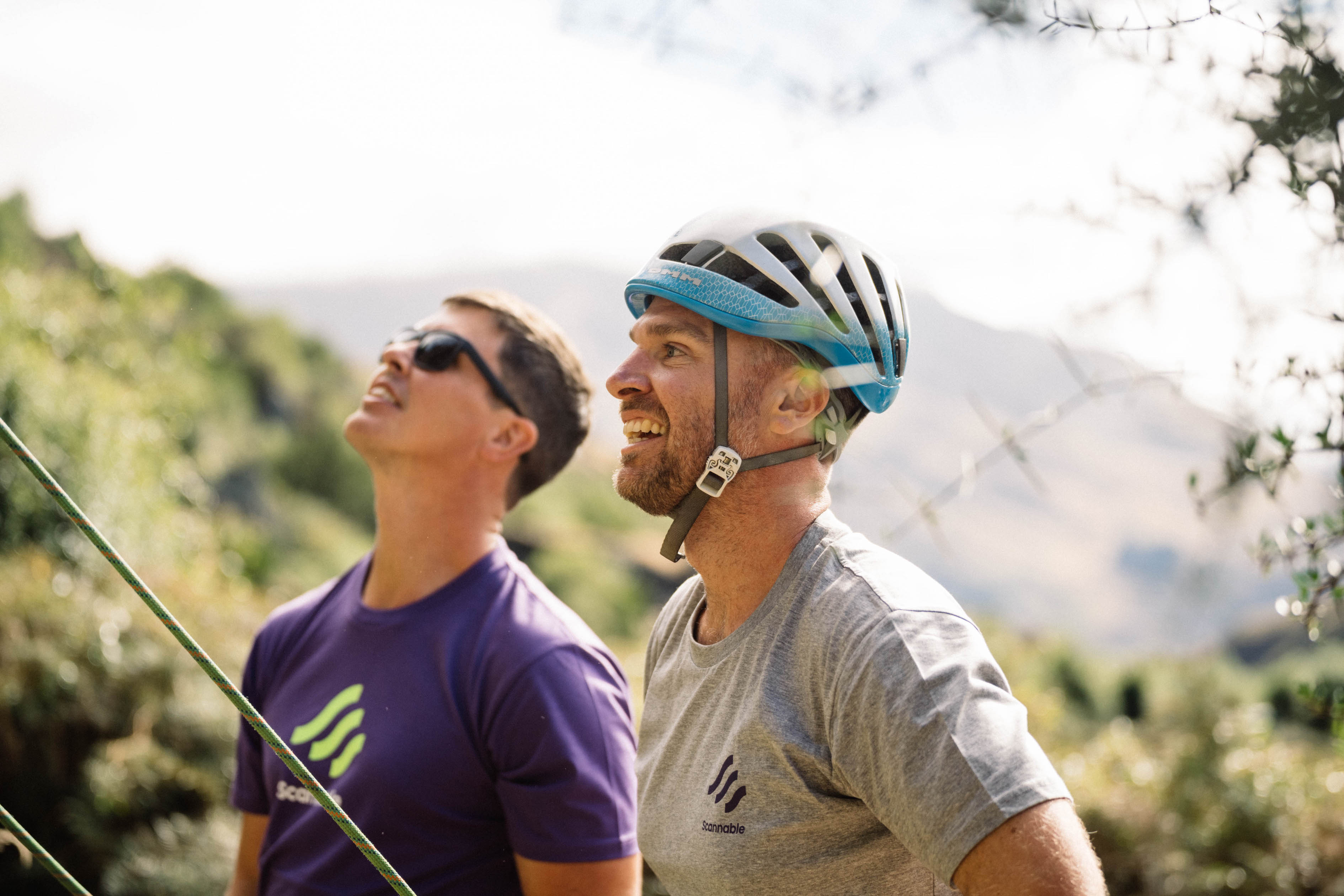
Yeah, we have an app. While we think it’s pretty neat (and you should definitely check it out if you haven’t already), we’re more than just an app. To get a little cliche on you, our app is the tip of the iceberg, but we have far more going on under the surface.
Climbing carabiners have their history rooted in a design thought to have been created for fire brigades in 1872. Until their development for climbing, the options for making yourself safe while climbing were neither particularly fast nor safe. Since the invention of the climbing carabiner, we have seen the invention and reinvention of all kinds of equipment specifically made for keeping us safe at height while at work or play.
Where’d this whole journey begin?
Founder Rob Stirling's connection to professional height safety came from working for DMM, an equipment manufacturer in the UK.
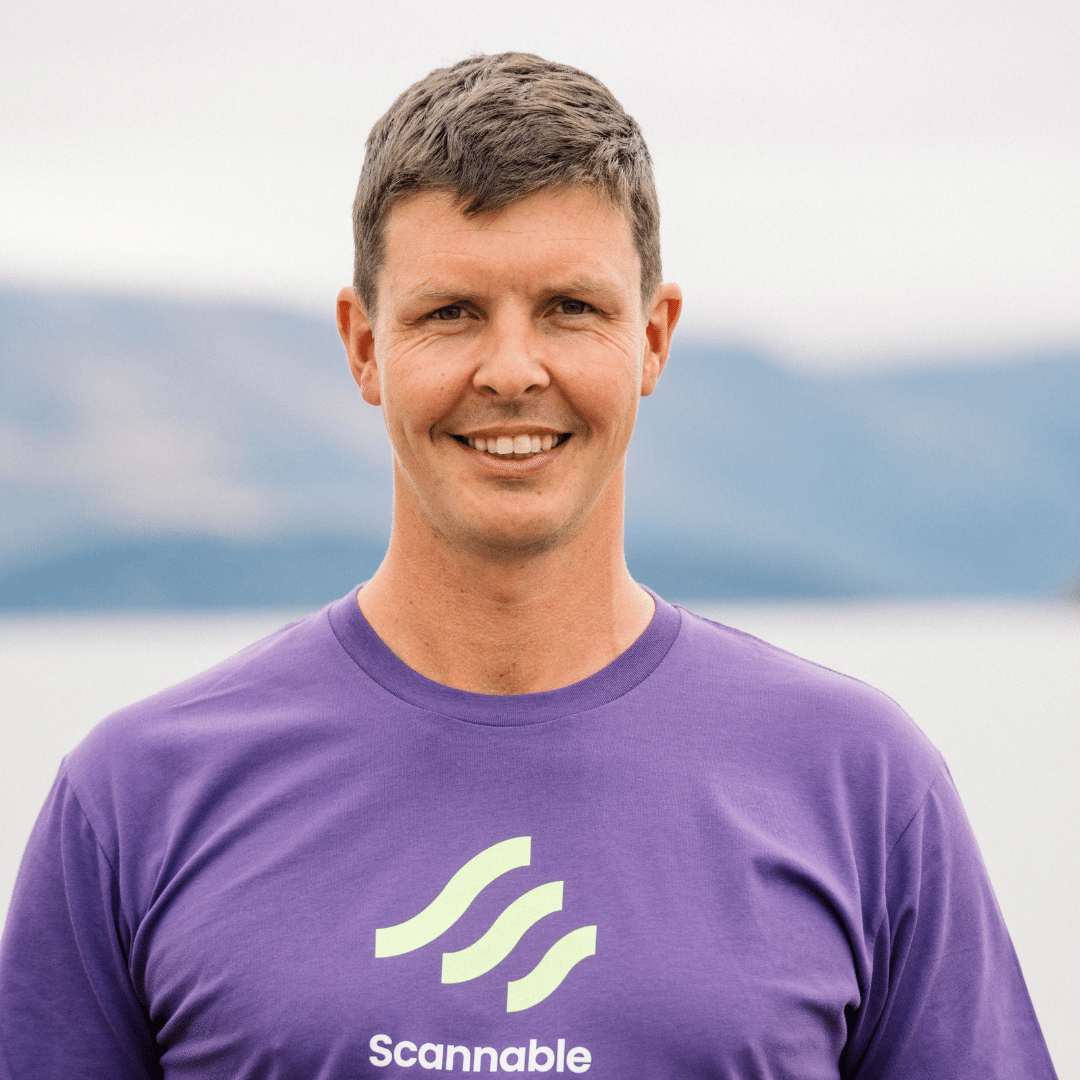
Co-founder Gene Dower has been a software engineer for over 15 years and was looking for a meaningful problem to apply his experience and skills.
.png)
Rob and Gene aligned on both being adventurous, risk managing individuals with a desire to solve meaningful problems.
Equipment manufacturers are often focussed on solving mechanical problems. They are innovative in the practical issues faced in equipment design, which uses engineering to solve problems.
It became clear to Rob that there was no clear way for the end users and owners of equipment to manage their equipment.
The primary concern with safety at height is that in order to make yourself safe, you need equipment. The reality of working at height today is that you actually can’t use the equipment without having the information that’s behind that equipment.
While there are still many mechanical issues to solve, it struck Rob that there was a big problem around actually accessing the data relative to the equipment and its use.
Rob began focussing on this problem, and developed the world's first RFID embedded carabiner. This meant that people no longer had to read and type serial numbers; it was an opportunity to deliver the data behind the serial in a more efficient manner than the traditionally data-entry heavy method.
After the product launched, Rob had his ear firmly to the ground listening to feedback from the market about the new technology.
This feedback clearly showed that there was a need to access scannable technology and compliance information across all brands, not just one.
He also discovered that the RFID solution only fitted in with the manufacturing process of one brand, but an enduring solution really needed to be user focussed, rather than manufacturer focussed.
Rob recognised that the equipment user’s best interest lied in delivering what is needed in order to make their job better. This is when the idea of an interconnected platform became apparent, and he realised that this was not going to be deliverable by any single manufacturer. The solution would need to be built by a third party.
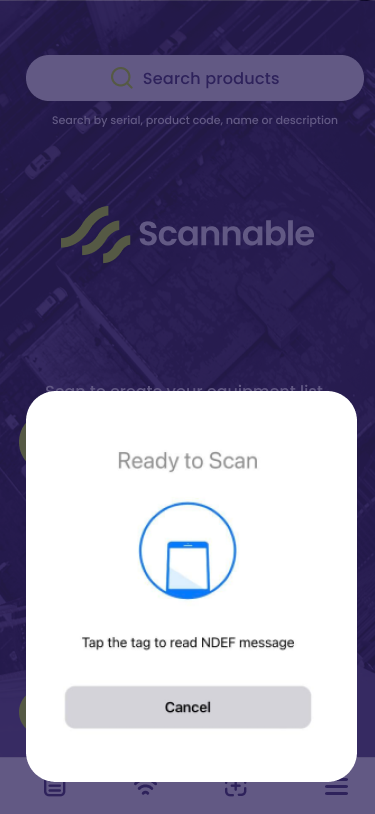
Our industry comes out of a non-digital culture, the people who do the real work in the industry are there to escape screen time.
However, the reality is that the industry has a data problem. Currently, data is isolated in the places it is recorded. Much helpful production information which evidences accountability for the production of PPE is recorded in places where product occurs, and it’s inaccessible to the wider public.
The data that does exist is isolated (or siloed, if you want to get techy). This means that the data is not very accessible, and it’s labour intensive to reference any of the information.
Currently, product information is pulled together from many different locations. Manufacturers think that a webpage is the best solution and latest technology for displaying product information, however there’s several drawbacks to this method of delivering the data. It’s an enormous job for people to reference, copy, and paste from a manufacturer’s website. Ultimately, this data is static - the data goes there, but it doesn’t flow out again. And once the product is obsolete at the manufacturer’s end, the page is removed from the website—even if your equipment is still in date.
Safety used to be the person behind the computer at the desk in the office. That’s where equipment management happened. Every person in the workforce today has a computer in their pocket, and so we can put answers to safety questions at the fingertips of every worker, regardless of the job. We put the information where the real work happens.
We all know that visual inspections of equipment aren’t enough. There simply isn’t enough data or information to make a good decision about the condition of the equipment and its safety simply by looking at it. You need more data. You need history. You need lifecycle data: how long has it been used, where, in what geography? Was it used in a marine environment? Alpine? Capturing this data is unviable at the moment.
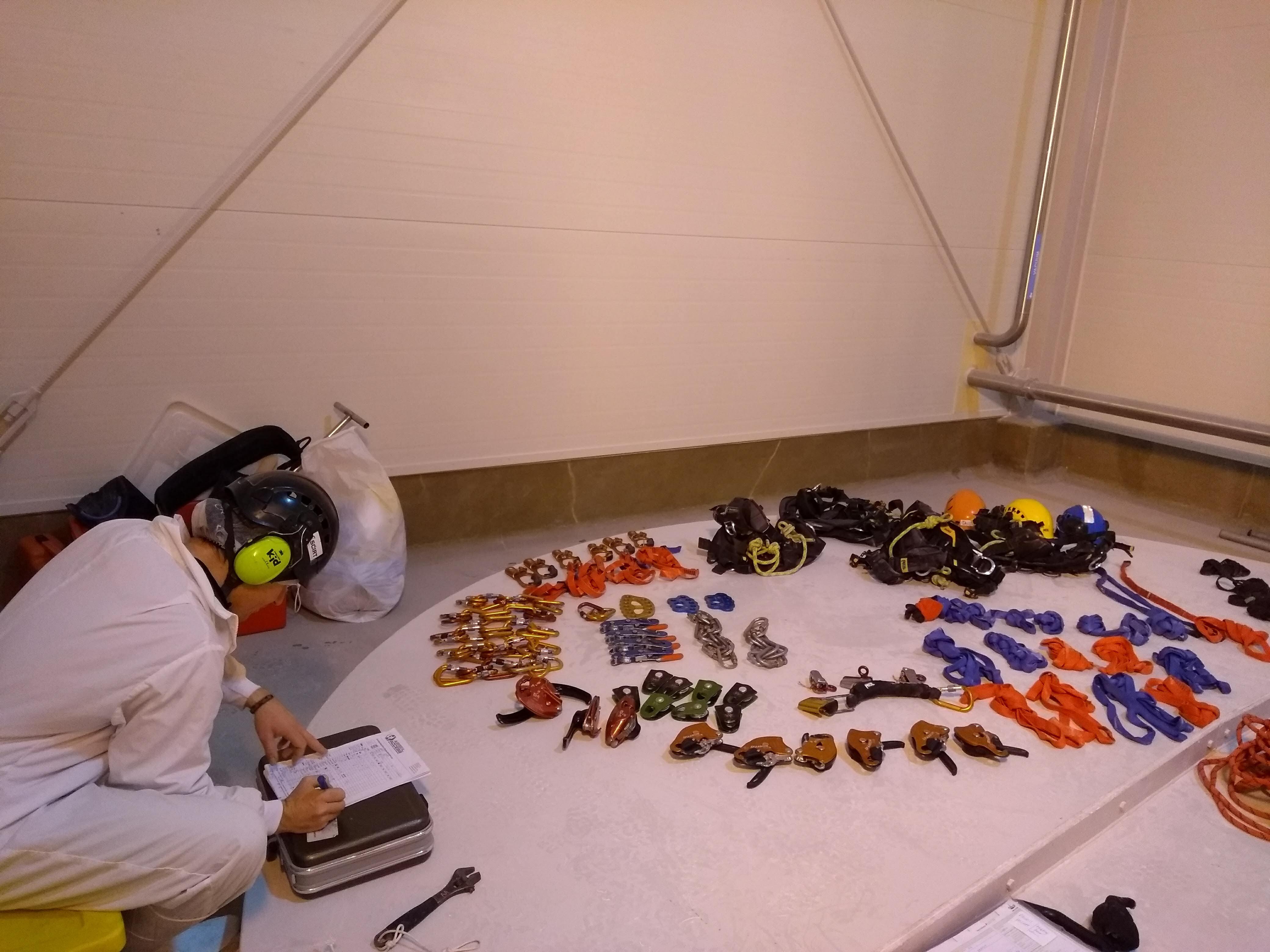
This a biiiiiig data problem: disconnected, poorly accessible data, blitzed into a thousand pieces and distributed through the industry, plus equipment use data that’s hard to capture.
This all starts with the manufacturer, or even the equipment designer or certifier. Manufacturers are responsible for recording information about the equipment, and there is a third party notified body/certifier which is also a source of information.
Currently it is not always possible to reference if the manufacturer has notified a body or if they have achieved a level of compliance.
We can see that there is an industry-wide value chain problem with data stuck in different places with different stakeholders, or not even captured.
Our vision is to build the tools for people to be able to capture, share and exchange this data, because it all informs better decisions about safety.
As our blog “The challenges of tracing rope” explains, the next data problem is rope. Our industry hinges around rope. At this point, maintaining traceability of rope is very labour intensive, and is ultimately ineffective. Connecting the data behind each master spool of rope with every length of rope in the marketplace is a data problem.
Capturing usage data is the next data problem that Rob identified.
It’s hard to know the history of rope, and that means that it’s hard to make decisions about rope. Throwing rope in the landfill is the current solution if you can’t answer the questions you need to about that rope.
We believe that the priority in our industry is safety, and we aim to make it viable to answer the questions about your equipment so that the answer isn’t always to just throw it out.
What does all of this mean? And why should you care?
We’re building the technology and sourcing the data so you don’t have to. We’re doing the hard work that’s boring so that you can answer the questions you need to keep you safe at work. And we can make it so that you can just tap your phone against the equipment and answer the question.
We know that it's tough, and that finding answers when you’re on site is, well, you know… We make it so that you don’t have to finger through hundreds of pages to find the answers to questions to make decisions quickly to get your job done.
We’re doing this to give you the tools to make it simple for you to do your job, safely. And without the paperwork. Our tools are the tip of the Scannable iceberg.
Yeah, we have an app. While we think it’s pretty neat (and you should definitely check it out if you haven’t already), we’re more than just an app. To get a little cliche on you, our app is the tip of the iceberg, but we have far more going on under the surface.
Climbing carabiners have their history rooted in a design thought to have been created for fire brigades in 1872. Until their development for climbing, the options for making yourself safe while climbing were neither particularly fast nor safe. Since the invention of the climbing carabiner, we have seen the invention and reinvention of all kinds of equipment specifically made for keeping us safe at height while at work or play.
Where’d this whole journey begin?
Founder Rob Stirling's connection to professional height safety came from working for DMM, an equipment manufacturer in the UK.
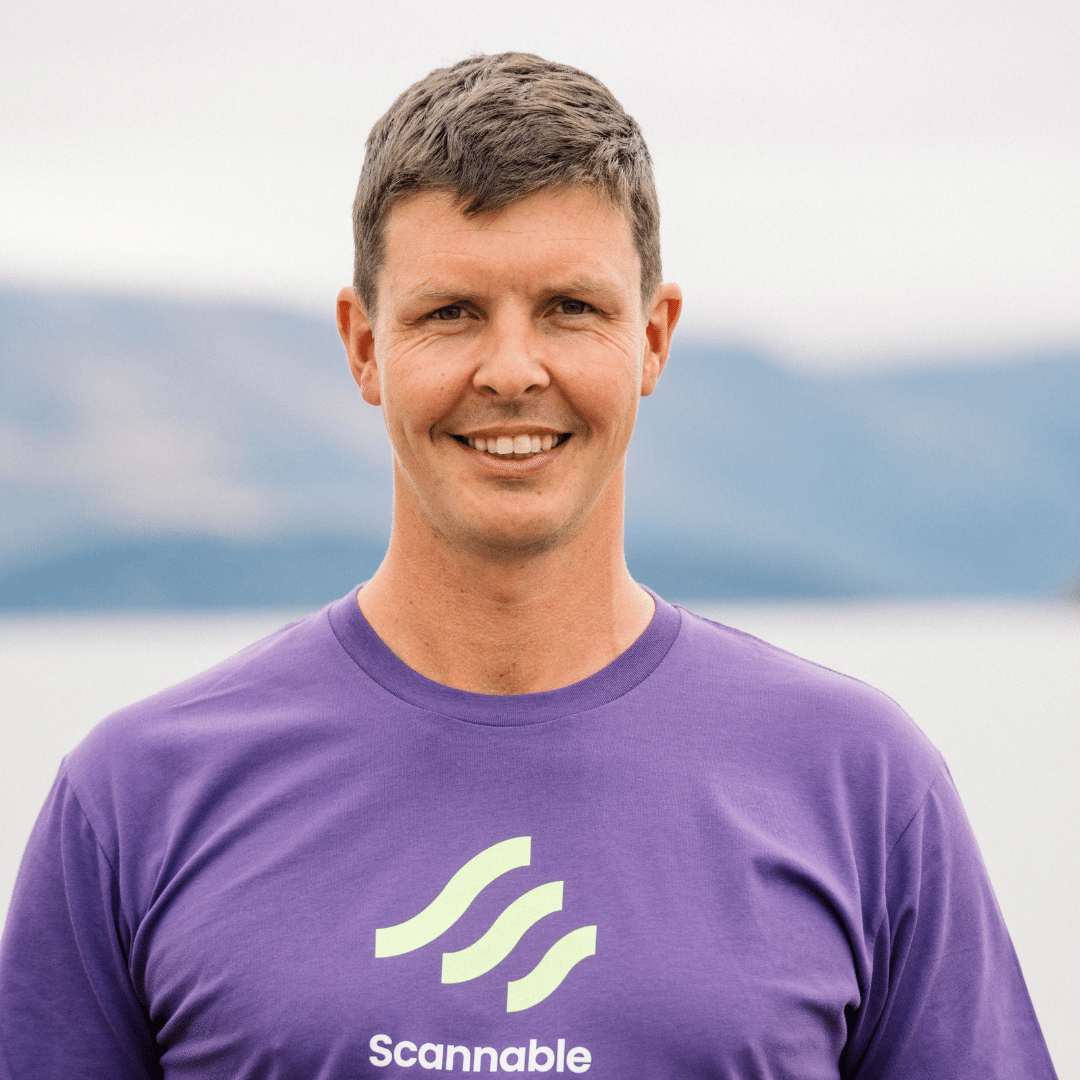
Co-founder Gene Dower has been a software engineer for over 15 years and was looking for a meaningful problem to apply his experience and skills.
.png)
Rob and Gene aligned on both being adventurous, risk managing individuals with a desire to solve meaningful problems.
Equipment manufacturers are often focussed on solving mechanical problems. They are innovative in the practical issues faced in equipment design, which uses engineering to solve problems.
It became clear to Rob that there was no clear way for the end users and owners of equipment to manage their equipment.
The primary concern with safety at height is that in order to make yourself safe, you need equipment. The reality of working at height today is that you actually can’t use the equipment without having the information that’s behind that equipment.
While there are still many mechanical issues to solve, it struck Rob that there was a big problem around actually accessing the data relative to the equipment and its use.
Rob began focussing on this problem, and developed the world's first RFID embedded carabiner. This meant that people no longer had to read and type serial numbers; it was an opportunity to deliver the data behind the serial in a more efficient manner than the traditionally data-entry heavy method.
After the product launched, Rob had his ear firmly to the ground listening to feedback from the market about the new technology.
This feedback clearly showed that there was a need to access scannable technology and compliance information across all brands, not just one.
He also discovered that the RFID solution only fitted in with the manufacturing process of one brand, but an enduring solution really needed to be user focussed, rather than manufacturer focussed.
Rob recognised that the equipment user’s best interest lied in delivering what is needed in order to make their job better. This is when the idea of an interconnected platform became apparent, and he realised that this was not going to be deliverable by any single manufacturer. The solution would need to be built by a third party.
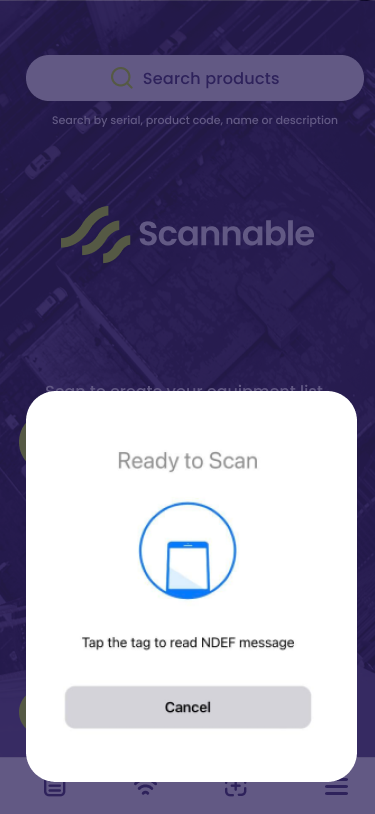
Our industry comes out of a non-digital culture, the people who do the real work in the industry are there to escape screen time.
However, the reality is that the industry has a data problem. Currently, data is isolated in the places it is recorded. Much helpful production information which evidences accountability for the production of PPE is recorded in places where product occurs, and it’s inaccessible to the wider public.
The data that does exist is isolated (or siloed, if you want to get techy). This means that the data is not very accessible, and it’s labour intensive to reference any of the information.
Currently, product information is pulled together from many different locations. Manufacturers think that a webpage is the best solution and latest technology for displaying product information, however there’s several drawbacks to this method of delivering the data. It’s an enormous job for people to reference, copy, and paste from a manufacturer’s website. Ultimately, this data is static - the data goes there, but it doesn’t flow out again. And once the product is obsolete at the manufacturer’s end, the page is removed from the website—even if your equipment is still in date.
Safety used to be the person behind the computer at the desk in the office. That’s where equipment management happened. Every person in the workforce today has a computer in their pocket, and so we can put answers to safety questions at the fingertips of every worker, regardless of the job. We put the information where the real work happens.
We all know that visual inspections of equipment aren’t enough. There simply isn’t enough data or information to make a good decision about the condition of the equipment and its safety simply by looking at it. You need more data. You need history. You need lifecycle data: how long has it been used, where, in what geography? Was it used in a marine environment? Alpine? Capturing this data is unviable at the moment.
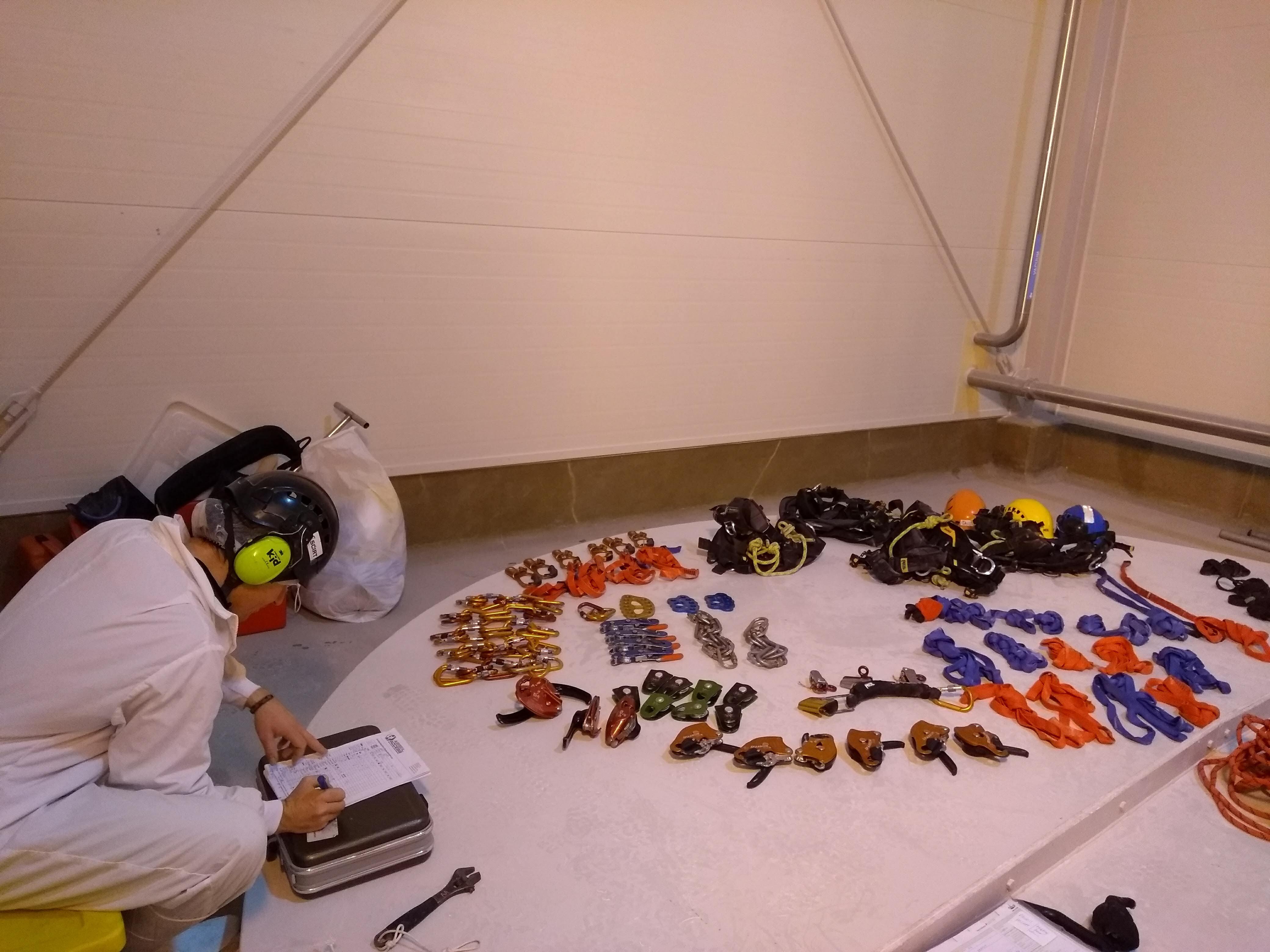
This a biiiiiig data problem: disconnected, poorly accessible data, blitzed into a thousand pieces and distributed through the industry, plus equipment use data that’s hard to capture.
This all starts with the manufacturer, or even the equipment designer or certifier. Manufacturers are responsible for recording information about the equipment, and there is a third party notified body/certifier which is also a source of information.
Currently it is not always possible to reference if the manufacturer has notified a body or if they have achieved a level of compliance.
We can see that there is an industry-wide value chain problem with data stuck in different places with different stakeholders, or not even captured.
Our vision is to build the tools for people to be able to capture, share and exchange this data, because it all informs better decisions about safety.
As our blog “The challenges of tracing rope” explains, the next data problem is rope. Our industry hinges around rope. At this point, maintaining traceability of rope is very labour intensive, and is ultimately ineffective. Connecting the data behind each master spool of rope with every length of rope in the marketplace is a data problem.
Capturing usage data is the next data problem that Rob identified.
It’s hard to know the history of rope, and that means that it’s hard to make decisions about rope. Throwing rope in the landfill is the current solution if you can’t answer the questions you need to about that rope.
We believe that the priority in our industry is safety, and we aim to make it viable to answer the questions about your equipment so that the answer isn’t always to just throw it out.
What does all of this mean? And why should you care?
We’re building the technology and sourcing the data so you don’t have to. We’re doing the hard work that’s boring so that you can answer the questions you need to keep you safe at work. And we can make it so that you can just tap your phone against the equipment and answer the question.
We know that it's tough, and that finding answers when you’re on site is, well, you know… We make it so that you don’t have to finger through hundreds of pages to find the answers to questions to make decisions quickly to get your job done.
We’re doing this to give you the tools to make it simple for you to do your job, safely. And without the paperwork. Our tools are the tip of the Scannable iceberg.